Purpose of Temperature Shock Test
Reliability environmental test In addition to high Temperature, low temperature, high temperature and high humidity, temperature and humidity combined cycle, temperature Shock (cold and hot Shock) is also a common test project, temperature shock Testing (Thermal Shock Testing, Temperature Shock Testing, referred to as: TST), the purpose of the temperature shock test is to find out the design and process defects of the product through the severe temperature changes that exceed the natural environment [temperature variability greater than 20℃/min, and even up to 30 ~ 40℃/min], but there is often a situation where the temperature cycle is confused with the temperature shock. "Temperature cycle" means that in the process of high and low temperature change, the temperature change rate is specified and controlled; The temperature change rate of "temperature shock" (hot and cold shock) is not specified (Ramp Time), mainly requires Recovery Time, according to the IEC specification, there are three kinds of temperature cycle test methods [Na, Nb, NC]. Thermal shock is one of the three [Na] test items [rapid temperature change with specified conversion time; medium: air], the main parameters of temperature shock (thermal shock) are: High temperature and low temperature conditions, residence time, return time, number of cycles, in high and low temperature conditions and residence time the current new specification will be based on the surface temperature of the test product, rather than the air temperature in the test area of the test equipment.
Thermal shock test chamber:
It is used to test the material structure or composite material, in an instant under the continuous environment of extremely high temperature and extremely low temperature, the degree of tolerance, so as to test the chemical changes or physical damage caused by thermal expansion and contraction in the shortest time, the applicable objects include metal, plastic, rubber, electronic.... Such materials can be used as the basis or reference for the improvement of its products.
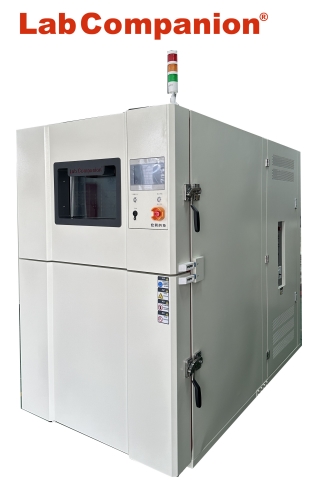
The cold and thermal shock (temperature shock) test process can identify the following product defects:
Different expansion coefficient caused by the stripping of the joint
Water enters after cracking with different expansion coefficient
Accelerated test for corrosion and short circuit caused by water infiltration
According to the international standard IEC, the following conditions are common temperature changes:
1. When the equipment is transferred from a warm indoor environment to a cold outdoor environment, or vice versa
2. When the equipment is suddenly cooled by rain or cold water
3. Installed in the outside airborne equipment (such as: automobile, 5G, outdoor monitoring system, solar energy)
4. Under certain transport [car, ship, air] and storage conditions [non-air-conditioned warehouse]
Temperature impact can be divided into two types of two-box impact and three-box impact:
Instructions: Temperature impact is common [high temperature → low temperature, low temperature → high temperature] way, this way is also called [two-box impact], another so-called [three-box impact], the process is [high temperature → normal temperature → low temperature, low temperature → normal temperature → high temperature], inserted between the high temperature and low temperature, to avoid adding a buffer between the two extreme temperatures. If you look at the specifications and test conditions, there is usually a normal temperature condition, the high and low temperature will be extremely high and very low, in the military specifications and vehicle regulations will see that there is a normal temperature impact condition.
IEC temperature shock test conditions:
High temperature: 30, 40, 55, 70, 85, 100, 125, 155℃
Low temperature: 5, -5, -10, -25, -40, -55, -65℃
Residence time: 10min, 30min, 1hr, 2hr, 3hr(if not specified, 3hr)
Temperature shock residence time description:
The Dwell Time of temperature shock in addition to the requirements of the specification, some will depend on the weight of the test product and the surface temperature of the test product
The specifications of the thermal shock residence time according to weight are:
GJB360A-96-107, MIL-202F-107, EIAJ ED4701/100, JASO-D001... Let's wait.
The thermal shock residence time is based on the surface temperature control specifications: MIL-STD-883K, MIL-STD-202H(air above the test object)
MIL883K-2016 requirements for [temperature shock] specification:
1. After the air temperature reaches the set value, the surface of the test product needs to arrive within 16 minutes (residence time is not less than 10min).
2. High temperature and low temperature impact are more than the set value, but not more than 10℃.
Follow-up action of IEC temperature shock test
Reason: The IEC temperature test method is best considered as part of a series of tests, because some failures may not be immediately apparent after the test method is completed.
Follow-up test items:
IEC60068-2-17 Tightness test
IEC60068-2-6 Sinusoidal vibration
IEC60068-2-78 Steady Humid heat
IEC60068-2-30 Hot and humid temperature cycle
Tin whisker (whisker) temperature impact test conditions finishing:
1. - 55 (+ 0 / -) 10 ℃ please - 85 (+ / - 0) 10 ℃, 20 min / 1 cycle (500 cycle check again)
1000 cycles, 1500 cycles, 2000 cycles, 3000 cycles
2. 85(±5)℃←→-40(+5/-15)℃, 20min/1cycle, 500cycles
3.-35±5℃←→125±5℃, dwell for 7min, 500±4cycles
4. - 55 (+ 0 / -) 10 ℃ please - 80 (+ / - 0) 10 ℃, 7 min reside, 20 min / 1 cycle, 1000 cycles
Thermal shock testing machine product features:
Defrosting frequency: defrosting every 600cycles [Test condition: +150℃ ~ -55℃]
Load adjustment function: The system can automatically adjust according to the load of the product to be tested, without manual setting
High weight load: Before the equipment leaves the factory, use aluminum IC(7.5Kg) for load simulation to confirm that the equipment can meet the demand
Temperature shock Sensor location: The air outlet and return air outlet in the test area can be selected or both can be installed, which conforms to the MIL-STD test specification. In addition to meeting the requirements of the specification, it is also closer to the impact effect of the test product during the test, reducing the test uncertainty and distribution uniformity.
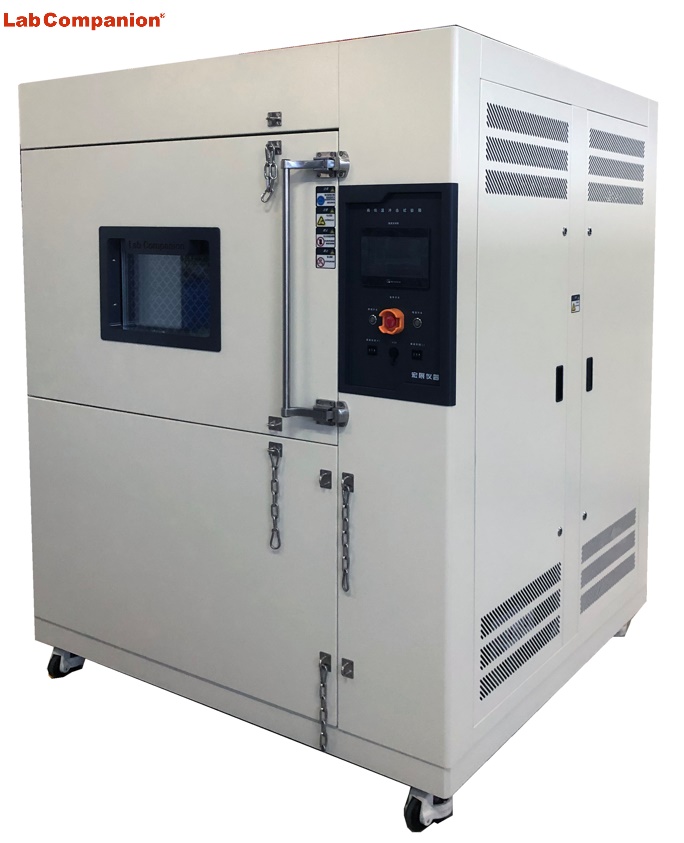