Introduction
With the continuous advancement of global industrialization, the demand for process pumps in the chemical industry continues to grow. As a critical fluid transfer device in chemical processes, chemical process pumps play a vital role in maintaining production continuity, improving efficiency, and ensuring safety and environmental compliance. This article will explore the classification, key features of current chemical process pumps, and the latest trends in market demand.
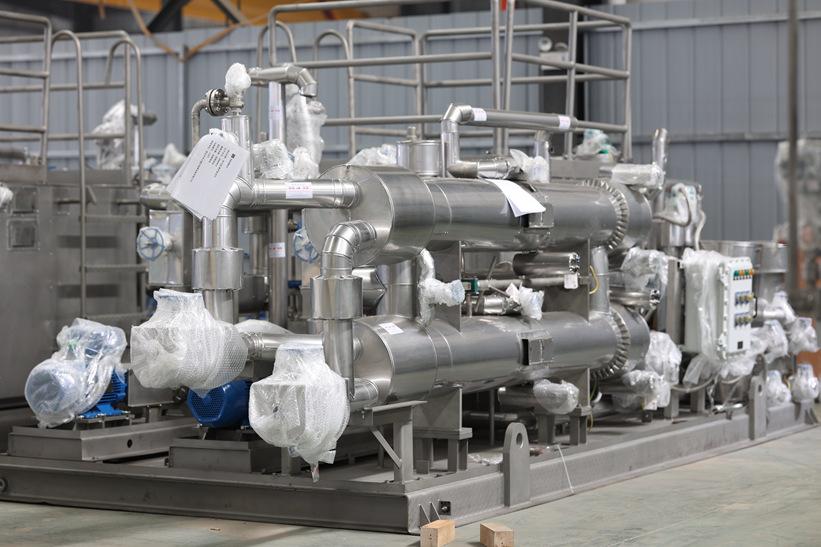
Classification of Chemical Process Pumps and Standards
1. Classification by Working Principle
- Centrifugal Pumps: Rely on the centrifugal force generated by a high-speed rotating impeller to transfer the fluid. These are the most common type of process pumps in the chemical industry, suitable for low-viscosity fluids with minimal particulates.
- Positive Displacement Pumps: Including gear pumps, screw pumps, and plunger pumps, these pumps transfer fluid through volume changes in the pump chamber, making them suitable for high-viscosity fluids or applications requiring precise metering.
- Magnetically Driven Pumps: Utilize magnetic couplings to transfer power, providing strong sealing capabilities. They are ideal for handling toxic, flammable, and explosive hazardous chemical fluids.
2. Classification by Material
- Metallic Pumps: Such as stainless steel and alloy pumps, are primarily used for transporting highly corrosive acidic and alkaline media. The choice of metallic material depends on the corrosiveness and temperature requirements of the medium.
- Non-Metallic Pumps: Such as fluoroplastic and ceramic pumps, offer superior corrosion resistance and are used for handling highly corrosive fluids, particularly in specialized applications where metallic pumps may not suffice.
3. Classification by Drive Type
- Electric Pumps: Driven by electric motors, these are the most common type of process pumps, suitable for various conditions, especially in continuous chemical operations.
- Pneumatic Pumps: Powered by compressed air, they are typically used in flammable or explosive environments, offering higher safety as they do not require electricity.
- Hydraulic Pumps: Driven by hydraulic systems, they are suitable for high-pressure applications, often used in processes requiring high delivery pressure.
4. Classification by Installation Method
- Horizontal Pumps: The pump shaft is installed horizontally, suitable for large spaces with easy maintenance, commonly found in large chemical plants.
- Vertical Pumps: The pump shaft is installed vertically, ideal for limited space, usually used for liquid transfer from underground tanks or deep wells.
2. Key Features of Chemical Process Pumps
1. Material Selection and Corrosion Resistance
Chemical process pumps are typically made from high-performance materials to withstand various complex chemical media. Common materials include stainless steel, Hastelloy, and titanium alloys, known for their excellent corrosion resistance, allowing them to operate long-term in harsh environments like strong acids and alkalis. Additionally, non-metallic materials such as fluoroplastics are widely used in specialized applications, offering exceptional corrosion resistance and wear properties.
2. High Efficiency and Energy Conservation
As energy conservation becomes a global trend, the efficiency of chemical process pumps has garnered significant attention. Modern process pumps, optimized in design and equipped with high-efficiency motors, effectively reduce energy consumption. In large-scale chemical facilities, these efficiency improvements not only lower operational costs but also reduce carbon emissions, aligning with the development direction of green chemistry.
3. Reliability and Durability
Operating in harsh industrial environments, chemical process pumps require high reliability and durability. Modern pumps often incorporate advanced sealing technologies and wear-resistant designs to extend service life and reduce maintenance frequency. Additionally, intelligent monitoring systems can monitor operational status in real-time, providing early warnings for potential failures, further enhancing system reliability.
3. Market Demand Analysis
1. Global Market Growth
According to market research reports, the global chemical process pump market is expected to maintain stable growth in the coming years. The Asia-Pacific region, driven by accelerated industrialization, especially in emerging markets like China and India, is experiencing the fastest growth in demand for chemical process pumps. In contrast, the European and North American markets focus primarily on technological upgrades and efficiency improvements, with high demand for high-performance, energy-efficient chemical pumps.
2. Green Chemistry and Sustainable Development
Stricter environmental regulations are accelerating the transition of chemical companies toward green chemistry, creating new market opportunities for energy-efficient chemical process pumps. Many companies are seeking low-energy, high-efficiency pump products to reduce their carbon footprint and comply with global environmental standards. Simultaneously, the concept of a circular economy is driving the development of the chemical pump market, requiring pumps with longer lifespans and higher resource utilization efficiency.
3. Regional Market Demand Differences
There are significant differences in the demand for chemical process pumps across different regions. The Asia-Pacific region, with its large-scale new projects, focuses on cost-effectiveness and bulk procurement. The European market places greater emphasis on technological advancement and environmental compliance, preferring high-efficiency, energy-saving pump products. The North American market, while maintaining high standards, is gradually moving towards smart equipment, with increasing demand for automation and intelligent monitoring systems.
Conclusion
As the global chemical industry evolves, the demand for chemical process pumps is becoming increasingly diversified. From material selection to energy efficiency improvements and regional market differences, the product features of chemical process pumps are closely linked to market demand. For chemical companies, selecting the right process pump can not only enhance production efficiency but also meet environmental requirements, helping them stay competitive in a rapidly changing market.
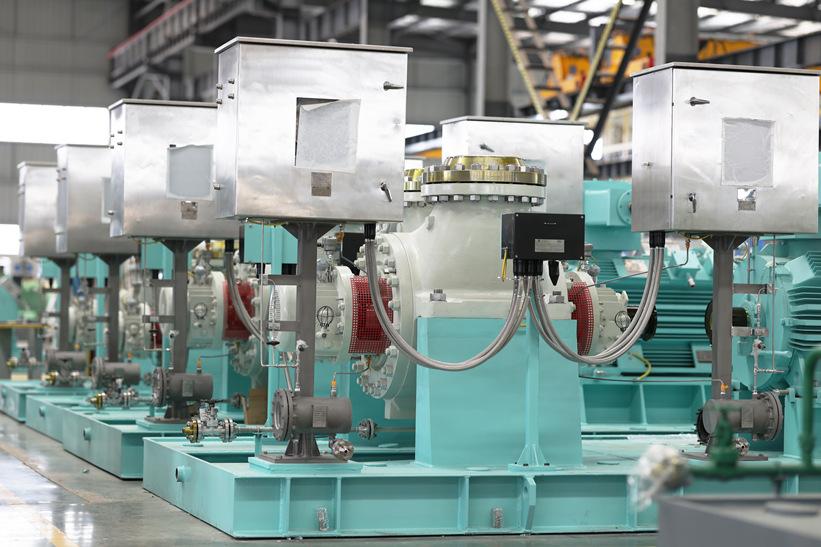
References
1. Market Research Report: "Global Chemical Process Pump Market Analysis," 2023 Edition.
2. Industry Analysis Article: "Technological Innovations and Applications of Chemical Process Pumps," published in 2022.
3. Academic Research: "Driving Factors of Chemical Process Pump Demand Growth in Emerging Markets," 2021.
4. Industry Trends Report: "Market Opportunities in Green Chemistry and Sustainable Development," 2023.
5. Internal Company Data: "Regional Market Demand Analysis for Chemical Pumps," Q2 2024 Report.