Lab-companion, whom we committed to delivering high-quality environmental testing equipment that serves the diverse needs of various industries. As industry leaders, we offer a range of products that ensure reliable testing and quality assurance for your operations.
Our thermal chambers can operate within a temperature range of 0°C to + 200°C and a humidity range of 5% to 98% RH. These chambers provide stable, long-term test conditions, making them compliant with the ICH Q1A guideline and ideal for a multitude of applications.
Learn more about thermal chambers below and how they can help ensure longevity and reliability for all your testing needs.
WHAT ARE TEMPERATURE CHAMBERS?
Temperature Chambers, often interchangeably referred to as Thermal Chambers, are specialized enclosures designed to create controlled thermal environments.
These chambers enable precise temperature simulations ranging from extreme cold to elevated heat to provide a stable setting where researchers can test products or materials for their resilience, durability, and overall performance.
The role of temperature chambers is pivotal in research and development phases across industries. Temperature chambers subject a product to various thermal conditions it is likely to encounter in the real world.
This simulative testing is essential to quality assurance processes, ensuring that products meet the safety and performance standards required.
By replicating various temperature scenarios, temperature chambers allow manufacturers and researchers to identify potential design flaws early, thus saving both time and resources in the long run.
HOW DO THERMAL CHAMBERS WORK?
A thermal chamber is a complex assembly of various components that create a controlled thermal environment. At its core are heating and cooling systems that can generate the required temperatures. These systems often use electric heaters for heating and a combination of compressors and refrigerants for cooling.
Insulation is critical to maintaining the chamber’s internal environment. Specialized materials help ensure that temperature changes are well-contained. Airflow management is also key; fans and ducts circulate the air to create uniform conditions throughout the chamber.
The “brains” of a thermal chamber are its controls and sensors. These are responsible for monitoring the temperature and ensuring it remains within set parameters.
Many thermal chambers utilize PID (Proportional-Integral-Derivative) controllers to maintain temperature accuracy. PID controllers continuously calculate the difference between the desired and current temperatures, making real-time adjustments to the heating and cooling systems to keep the temperature within a predefined range.
All these components come together to power a system that can simulate a wide range of temperature conditions, making thermal chambers invaluable tools in product development and quality assurance processes.
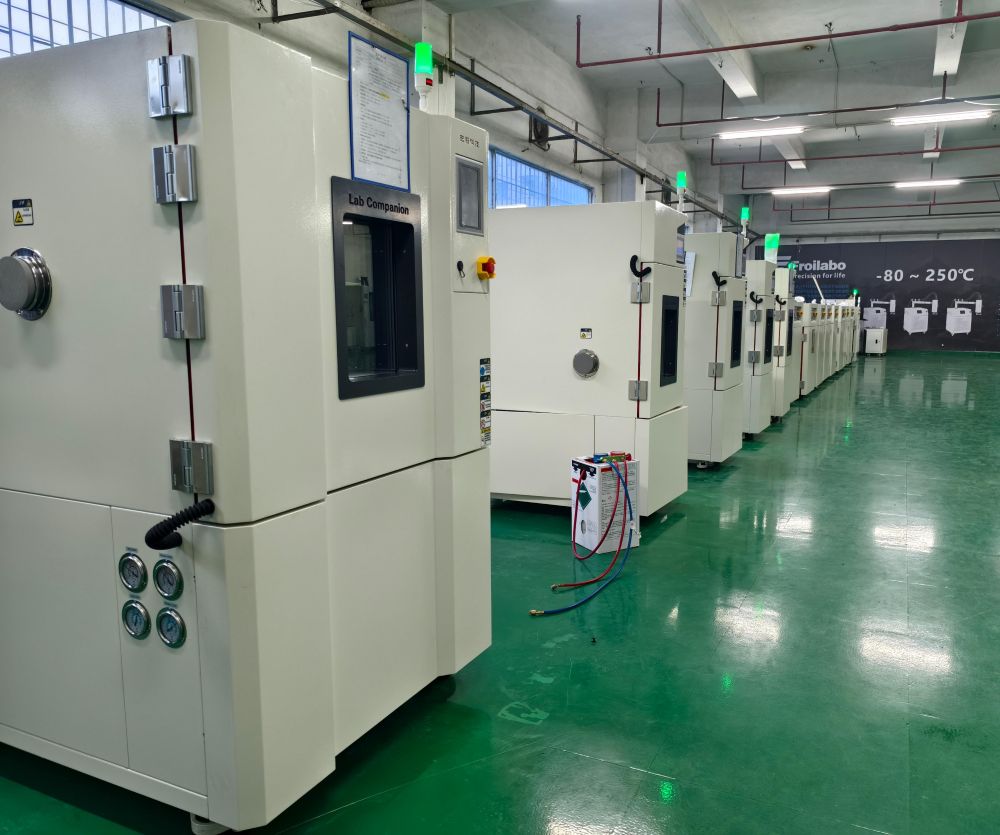
TEMPERATURE CHAMBERS: INDUSTRIES AND APPLICATIONS
Temperature or thermal chambers are versatile tools that find applications across numerous industries. Their role in simulating various temperature conditions makes them indispensable for research, development, and quality assurance.
In the automotive sector, thermal chambers test components like engines, batteries, and HVAC systems. These tests help manufacturers ensure that vehicles can withstand extreme weather conditions, be it the cold of a frigid winter or the heat of a scorching desert.
For electronics, thermal chambers help ensure that devices like smartphones, laptops, and other gadgets operate effectively across various temperatures. For example, humidity condition tests are crucial for consumer satisfaction and safety, ensuring that devices won’t fail when exposed to extreme conditions.
- MEDICAL/PHARMACEUTICAL INDUSTRY
In the medical and pharmaceutical sectors, thermal chambers are essential for testing the stability and shelf-life of drugs and the reliability of medical devices. From vaccines to pacemakers, stability testing ensures these critical products operate safely and efficiently.
The aerospace sector often utilizes thermal chambers to test components that will endure extreme conditions in space or high-altitude flight. Aerospace manufacturers must test everything from materials used in aircraft bodies to the electronics in satellite systems to ensure resilience, reliability, and safety.
TYPES OF TESTS CONDUCTED IN THERMAL CHAMBERS
Thermal chambers are highly versatile and capable of performing an array of tests that simulate different environmental conditions. Some of the most common tests include:
- Thermal Cycling: This test exposes the subject to various temperatures, oscillating between cold and hot conditions, to assess its resilience and pinpoint any potential weaknesses.
- Thermal Shock: Here, the product is subjected to abrupt temperature changes to evaluate its ability to withstand sudden temperature fluctuations, a frequent cause of failure for numerous devices.
- High-Temperature Testing: This test assesses the subject’s ability to function in extremely high temperatures, often for extended periods.
- Low-Temperature Testing: This test evaluates how well a product can function at cold temperatures, often freezing or below.
- Temperature Humidity Testing: This test combines both temperature and humidity variables. While thermal chambers mainly focus on temperature conditions, they can often incorporate humidity settings to some extent. This is where they differ from humidity chambers, which primarily control moisture levels.
If you’re looking for a chamber that controls temperature and humidity, Lab-companion offers specialized chambers that provide the best of both worlds.
EXPLORE LAB-COMPANION’S TEMPERATURE CHAMBERS
When it comes to reliability and efficiency, our product catalog stands out for several compelling reasons:
- Accelerated Testing: With advanced heating and cooling systems, our chambers are designed for rapid temperature cycling, allowing for quicker test completion without compromising the accuracy of results.
- Reliable Results: The chambers are equipped with cutting-edge sensors and controls, ensuring that you receive consistent and reliable data throughout the testing process.
- Cost-Efficiency: Investing in a high-quality temperature chamber like those offered by us can significantly reduce long-term testing costs. Their durability and low maintenance requirements make them a cost-effective choice for any organization.
- Customizable Settings: Lab-companion offers a high degree of customization, allowing you to tailor the testing environment according to the specific needs of your product, further enhancing the accuracy of your tests.
Understanding the ins and outs of temperature chambers is essential for anyone involved in product development, research, or quality assurance across various industries.
These chambers play a crucial role in simulating different environmental conditions, enabling organizations to rigorously test their products for safety, reliability, and durability. From automotive and electronics to aerospace and pharmaceuticals, the applications are as diverse as they are crucial.
If you’re looking to elevate your testing processes, you can’t afford to overlook the value of a top-tier temperature chamber.
Contact us at the bottom of the page for more information.